The Main Determinants of Concrete Plant Prices
When it comes to purchasing a concrete plant for construction projects, one of the first questions most buyers have is: What determines the price of a concrete plant? Concrete plants, ranging from large stationary models to portable concrete batching plants, can have a wide price range depending on various factors. Understanding the main determinants of concrete plant prices is crucial for making an informed purchasing decision. In this article, we will explore the key factors that influence the cost of concrete plants.
Key Factors Influencing Concrete Plant Prices
Several aspects play a role in determining the price of a concrete plant(planta de hormigon en venta). These factors include the plant's type, production capacity, features, and the manufacturer's reputation. Additionally, geographical location, shipping costs, and installation requirements can also affect the final price. Let's break down these factors for a clearer understanding.
1. Type of Concrete Plant
The type of concrete plant is one of the most significant determinants of the overall cost. Concrete plants can be categorized into two main types: stationary concrete plants and portable concrete batching plants.
Stationary Concrete Plants
Stationary concrete plants are designed to be set up at a fixed location and are ideal for large-scale construction projects. They offer high production capacity, reliability, and consistent performance, but they also come with a higher price tag. These plants are built to handle continuous, high-volume production, which increases their cost due to the specialized equipment and infrastructure needed for operation.
Portable Concrete Batching Plants
Portable concrete batching plants are a more flexible and mobile solution, suitable for smaller or temporary projects. These plants are compact, can be easily transported, and are designed for quick setup and relocation. While portable plants(planta dosificadora de concreto portatil) typically have a lower initial investment compared to stationary plants, they may have a higher cost per unit of production because of their mobility and smaller capacity. However, their convenience and ability to be used for multiple projects can offer long-term savings.
2. Production Capacity
The production capacity of a concrete plant is another key factor influencing its price. Larger plants that produce more concrete per hour or per day generally come with higher prices. For example, a high-capacity concrete batching plant for sale that can handle thousands of cubic meters of concrete per day will cost significantly more than a plant with a lower capacity designed for smaller-scale operations.
Production capacity is directly related to the size of the plant, the number of mixing units, and the storage capacity for raw materials. Larger plants require more sophisticated infrastructure, additional equipment for efficient batching and mixing, and stronger materials to handle the increased workload. For contractors working on large-scale projects, the investment in a high-capacity plant might be justified, while smaller projects may benefit from more compact, lower-capacity plants.
3. Features and Technology
The level of technology and features incorporated into a concrete plant can significantly impact its price. Modern concrete plants come with a variety of advanced features, including automated batching systems, digital controls, and sophisticated monitoring tools that improve production efficiency, reduce human error, and ensure precise batching. These features contribute to the overall cost of the plant.
For example, plants equipped with automated control systems or advanced mixing technologies may come with a higher price, but they can also reduce labor costs and improve the consistency and quality of the concrete produced. Conversely, simpler plants without such technology may be more affordable but may require more manual labor and may be prone to inconsistency in product quality.
4. Manufacturer and Brand Reputation
The manufacturer and brand of the concrete plant(planta de concreto en Perú) play a crucial role in determining the price. Established brands with a reputation for producing high-quality, durable equipment often charge a premium for their products. These manufacturers typically provide better after-sales support, warranties, and service options, which can justify the higher price. Buyers are often willing to invest more in a well-known brand because of the reliability and long-term performance of the equipment.
On the other hand, lesser-known manufacturers may offer more budget-friendly options, but these plants may not come with the same level of customer support or the same longevity as those from more reputable manufacturers. For some buyers, the lower initial cost of purchasing from a lesser-known brand may be appealing, but it's important to consider the potential for increased maintenance costs or downtime.
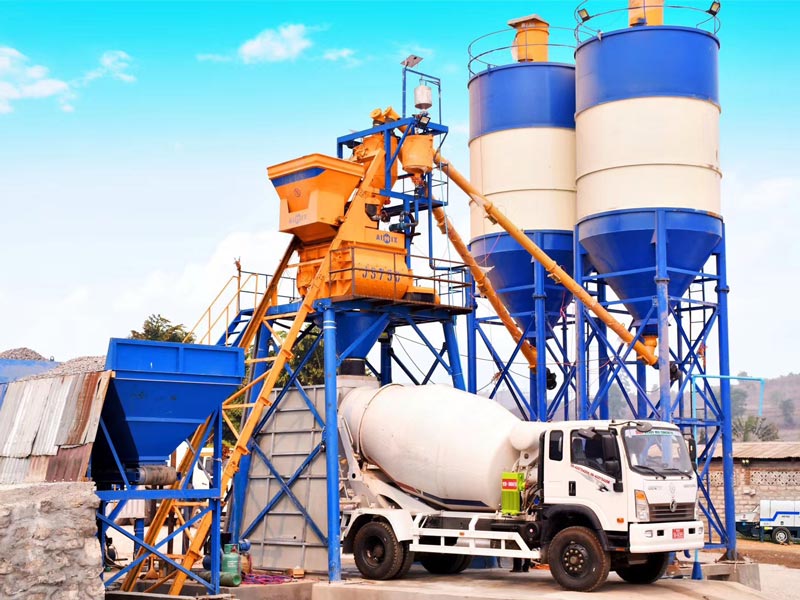
5. Shipping and Installation Costs
Another often-overlooked cost factor is the expense associated with shipping and installing the plant. Concrete plants, especially large stationary models, require significant logistics support for transportation. Shipping costs can vary depending on the size of the plant, the distance it needs to travel, and whether it needs to be disassembled and reassembled on-site.
In addition to transportation, installation costs can also add to the overall price. Installing a stationary concrete plant requires specialized labor and equipment, which can increase the cost. For portable concrete batching plants, the installation process is generally faster and less expensive, as they are designed to be quickly set up and relocated.
6. Geographic Location
The location of the buyer and the plant's manufacturer can also influence the price. Transportation costs for both shipping the plant to the buyer's site and the delivery of raw materials can be higher in certain locations, especially if the plant needs to be transported internationally. Additionally, local regulations and labor costs can affect the final price, especially when the plant must meet specific environmental or safety standards.
7. Additional Costs
Lastly, buyers should consider additional operational and maintenance costs over the life of the plant. While a concrete batching plant for sale may appear affordable upfront, ongoing maintenance, spare parts, and operational costs can add up over time. Investing in a plant with lower operational costs, such as energy-efficient systems or reduced wear and tear on components, can help minimize these expenses in the long run.
Conclusion
The price of a concrete plant is influenced by multiple factors, including the type of plant, production capacity, technology, and brand reputation. Buyers should carefully evaluate their specific project requirements, production volume, and budget to choose the right concrete plant for their needs. Whether opting for a stationary model for large-scale operations or a portable concrete batching plant for mobility and flexibility, understanding the main determinants of concrete plant prices can help ensure a cost-effective investment in construction equipment. By considering these factors, contractors can make informed decisions that not only meet their current needs but also provide long-term operational savings.